Introduction
In modern warehouse operations, efficiency and safety are paramount. The use of innovative equipment can significantly enhance both. This case study explores how IBC Pallet Lifters have revolutionized warehouse operations by improving efficiency and safety standards.
Challenges in Warehouse Operations
Warehouse operations often involve handling heavy and cumbersome loads. Traditional methods of moving and lifting these loads can be time-consuming and pose significant safety risks. The primary challenges include:
- Manual Handling Risks: Lifting and transporting heavy loads manually can lead to musculoskeletal injuries among workers.
- Time Consumption: Traditional pallet handling methods are often slow, leading to reduced productivity.
- Operational Inefficiencies: Inefficient load handling can result in delays and increased operational costs.
Introduction of IBC Pallet Lifters
IBC Pallet Lifters were introduced to address these challenges. These lifters are designed to handle intermediate bulk containers (IBCs) efficiently. Key features include:
- Ergonomic Design: The lifters are designed to minimize physical strain on workers, reducing the risk of injuries.
- Enhanced Load Capacity: They can handle heavy loads with ease, ensuring smooth and efficient operations.
- Versatility: IBC Pallet Lifters are compatible with various types of pallets, making them suitable for diverse warehouse needs.
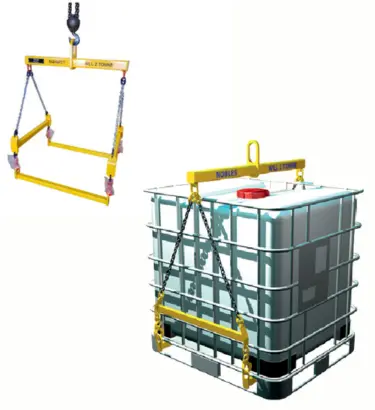
Impact on Efficiency
The introduction of IBC Pallet Lifters had a profound impact on warehouse efficiency. Some notable improvements include:
- Increased Productivity: The lifters enabled faster handling of IBCs, significantly reducing the time required for loading and unloading.
- Reduced Downtime: With the ability to handle heavy loads effortlessly, there was less downtime due to equipment failure or worker fatigue.
- Optimized Workflow: The ergonomic design and ease of use of the lifters streamlined the workflow, leading to more organized and efficient operations.
Impact on Safety
Safety was a primary concern addressed by the IBC Pallet Lifters. The improvements in safety standards included:
- Reduced Injury Rates: The ergonomic design minimized the physical strain on workers, leading to a decrease in work-related injuries.
- Improved Workplace Morale: With enhanced safety measures, workers felt more secure and motivated, contributing to a positive work environment.
- Compliance with Safety Regulations: The use of advanced lifting equipment ensured compliance with safety standards and regulations, reducing the risk of legal issues.
Conclusion
The implementation of IBC Pallet Lifters in warehouse operations resulted in significant improvements in both efficiency and safety. By addressing the challenges associated with traditional load handling methods, these lifters have become an essential tool for modern warehouses. The case study highlights the importance of investing in innovative equipment to enhance operational efficiency and ensure a safe working environment.
Visit for more information : https://www.hfs-safety.com/product/ibc-lifter/